Mobile Supply Chain Management
Increase Your Efficiency of Material Management
Designed to meet the needs of the on-the-move, dispersed workforce common in today’s business environments, Infor’s Mobile Supply Chain Management (MSCM) module enables companies to enhance receiving, delivery and inventory management processes by automating data collection where the work is done. MSCM increases the productivity of materials staff in receiving docks, warehouses, storerooms and par locations, by using handhelds to capture and transmit data via wireless connections.
Upgrade to MSCM Version 10
RPI’s priority is to ensure that you are getting the most out of your system. We can assist you in upgrading your Infor Mobile Supply Chain Management software to its newest version. Recent enhancements include:
- Newly formatted User Interface
- Increased functionality for Point-of-Use system, with enhanced support for clinical departments
- Par & Cycle Counting performance improvement
- Support of new FedEx bar code
- Improved Infor Environment and Enterprise Application support
How can RPI help?
As an Infor’s Alliance Partner in , RPI assists with the installation, implementation and deployment of Infor’s full MSCM Suite including Par & Cycle Counting, Receiving and Delivery, Surgical Instrument Management, and Point of Use.
Our MSCM certified consultants leverage their knowledge of procure-to-pay business processes in various industries to fully capture the benefits of this new technology. RPI helps your organization get the most out of Mobile Supply Chain.
We offer full cycle implementation assistance, including system installation and configuration, custom end-user training, system testing, deployment and go-live support at reasonable costs.
RPI also provides on-demand consultations and support to help organizations in a troubleshooting crunch meet their deadlines.
Par & Cycle Counting
Infor’s MSCM Par & Cycle Counting replaces the previous versions of handheld integrators with new and improved functionality. By automating, streamlining and improving inventory and par counting processes, Par & Cycle Counting vastly improves manual processes that are time and labor intensive and can sometimes lead to inaccurate counts.
Uses Newest Wireless Technologies
- Ability to scan bar codes to identify shelf locations and enter item numbers
- Short sync times, MS Windows CE platform for labels
- Performance, productivity and activity tracking
- Ability to view all items on part (IC81) on item view screen
- Ability to enter amount above par quantity
- Ability to view Quantity on
- Order while entering counts
- Pick multiple pars in one sweep (wireless)
Minimizes paperwork and batching, streamlining data entry
- Synchronizes counts in real time when using wireless
- Reduces the amount of time needed to conduct inventory and par counting
- Records counts faster and more accurately resulting in expedited replenishment
- Allows a greater number of Pars to be counted at one time than old handhelds
- Maintains better stock levels
- Optimizes staff levels through reduced supply chain costs
- Tracks activity, increasing accountability
- Improves replenishment and inventory accuracy
Receiving & Delivery (RAD)
Infor’s Receiving and Delivery MSCM module allows users to perform package receiving (PO30), picking (WH32) and stock issues and returns (IC21) through a handheld. This technology improves delivery management by organizing delivery routes and allows for greater accountability with signature capture. It allows receivers to track Non PO receipts and provides departments with self service tracking.
Dock logging
- Confirms delivery of packages compared to carrier’s manifest, allowing you to resolve discrepancies immediately while the driver is still on site
- Record the exact time of delivery for both PO and non-PO deliveries
- Miscellaneous Receiving (non-PO)
- Designate a tracking number and scan it into RAD to track the movement of the package
- Indicate specific delivery directions for staff
- PO Receiving
- Receive PO items via handheld
- Update PO30 automatically through transfer of data from RAD to
Procurement Picking
- Pick inventory items ordered via Requisitions and enter shipping feedback
- Track deliver of those items
Issues
- Issue or return items for any department set up as a requesting location
Delivery
- Deliver both PO and Miscellaneous (Non-PO) Receipt
- Track all events during the life cycle of the packages delivery
Tracking
- Empower end users by allowing them to check the status of their packages once scanned at the receiving dock
- Enable MM staff to have increased visibility of their deliveries and where they are located
Benefits:
- Reduced risk of losing packages
- Increased visibility of goods in the system
- Ability to process and track non-PO deliveries
- Save paper by eliminating the need to print receiving and delivery tickets
- Ability to issue while standing at shelf reduces inventory shrinkage
- Increased inventory accuracy and replenishment urgical
- Instrument Management (SIM)
Surgical Instrument Management (SIM)
Surgical Instrument Management (SIM) is a solution that configures, compiles and tracks case carts through the sterilization, picking, usage and decontamination life-cycle. It can be implemented as a stand along solution or as part of MSCM.
- Online tray configuration with images
- Tracking loaner trays and peel packs
- Detailed assembly instructions
- Online instrument catalog and tray lists
- Capture and track individual instrument IDs
- Capture sterilization data
- Productivity reporting for all activities
Reduce instrument and tray inventory Costs savings:
- Improved instrument utilization rates
- Increased staff productivity in assembling trays/carts
- Improve service
- Increase productivity and accountability at every stage of life cycle
Point of Use
Designed for use by nurses, materials technicians, data entry clerks, nurse supervisors and materials supervisors, Infor’s Point of Use allows organizations to automate the Supply Chain, Financial and Patient Billing processes connected with chargeable patient consumables at the point of care/use.
- Utilizes touch screen/scanner, handheld, or desktop models, so staff can efficiently execute patient recording processes in stockrooms, on supply carts, or at desks.
- Simplified charge collection process and eliminates steps for replenishing stock.
- Elimination of patient charge labels
- Avoids and reduces the need for expensive cabinet-based systems and custom interfaces to Infor.
- Increases patient billing revenue by reducing lost charges and charge errors.
- Frees up time to focus more fully on patients and providing excellent care, while capturing untapped revenue to boost the financial health of your facility.
Follow us online for faster access to announcements, knowledge base updates, and upcoming events!
Entire Knowledge Base
All Products, Solutions, & Professional Services
Contact Us to Get Started
Don’t Just Take Our Word for it!
See What Our Clients Have to Say

Denver Health
“RPI brought in senior people that our folks related to and were able to work with easily. Their folks have been approachable, they listen to us, and they have been responsive to our questions – and when we see things we want to do a little differently, they have listened and figured out how to make it happen. “
Keith Thompson
Director of ERP Applications
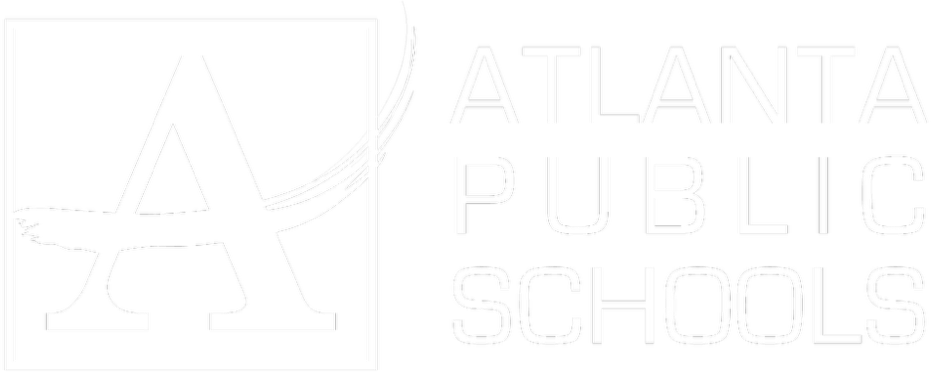
Atlanta Public Schools
“Prior to RPI, we were really struggling with our HR technology. They brought in expertise to provide solutions to business problems, thought leadership for our long term strategic planning, and they help us make sure we are implementing new initiatives in an order that doesn’t create problems in the future. RPI has been a God-send. “
Skye Duckett
Chief Human Resources Officer
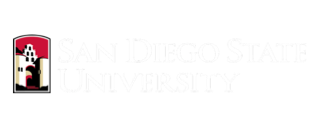
San Diego State University
“Our favorite outcome of the solution is the automation, which enables us to provide better service to our customers. Also, our consultant, Michael Madsen, was knowledgeable, easy to work with, patient, dependable and flexible with his schedule.”
Catherine Love
Associate Human Resources Director
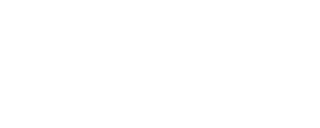
Bon Secours Health System
“RPI has more than just knowledge, their consultants are personable leaders who will drive more efficient solutions. They challenged us to think outside the box and to believe that we could design a best-practice solution with minimal ongoing costs.”
Joel Stafford
Director of Accounts Payable
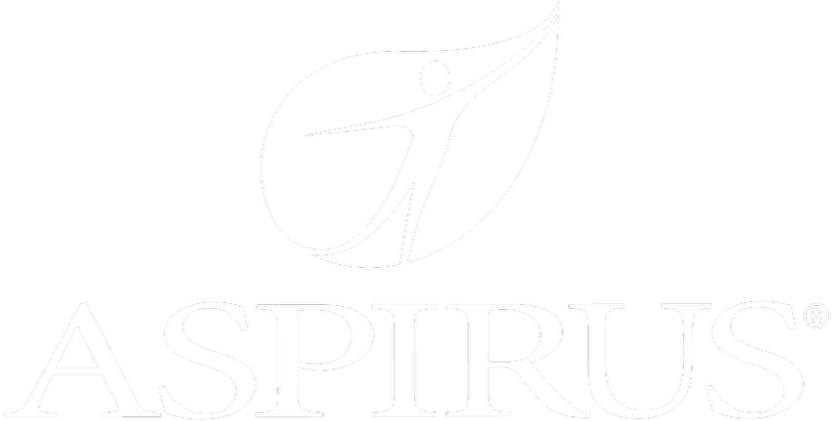
Aspirus
“Our relationship with RPI is great, they are like an extension of the Aspirus team. When we have a question, we reach out to them and get answers right away. If we have a big project, we bounce it off them immediately to get their ideas and ask for their expertise.”
Jen Underwood
Director of Supply Chain Informatics and Systems
Our People are the Difference
And Our Culture is Our Greatest Asset
A lot of people say it, we really mean it. We recruit good people. People who are great at what they do and fun to work with. We look for diverse strengths and abilities, a passion for excellent client service, and an entrepreneurial drive to get the job done.
We also practice what we preach and use the industry’s leading software to help manage our projects, engage with our client project teams, and enable our team to stay connected and collaborate. This open, team-based approach gives each customer and project the cumulative value of our entire team’s knowledge and experience.